Process-structure-property predictions for metal additive manufacturing
We developed a multi-scale high performance computing framework for the multiphysics additive manufacturing process-structure-property (PSP) predictions. A hyper reduced order model (HROM) is developed for rapid predictions of the temperature history and melt pool shapes during a laser powder bed fusion process. The HROM can predict accurately the temperature evolution and melt pool dimensions during the process with significant speedups over full order models. The predicted temperature evolution can be used to predict the residual stress in the manufacturing process with a newly developed eXtended tensor decomposition (XTD) nonlinear model reduction method. Based on the scanning electron microscope (SEM) images, the microstructures of resultant materials were generated and used for the final mechanical property prediction. The predicted stress-strain curve from our numerical models were validated by the NIST-led Additive Manufacturing Benchmark Test Series.
Part-scale precess modeling
Goals: efficient and accurate predictions of temperature evolution, residual stress, part distortion, etc.
Adaptive hyper reduced order thermal fluid analysis for temperature and melt pool predictions [Lu et al. CMAME, 2020]
Extended tensor decomposition based elastoplastic analysis for residual stress and strain predictions [Lu et al. CMAME, 2024]
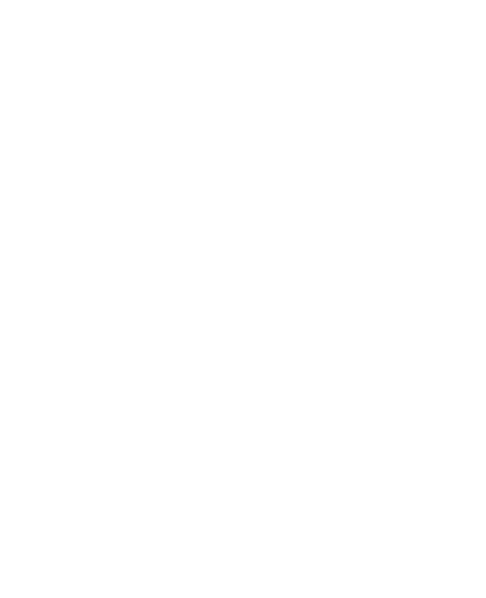
Microstructure-scale modeling
Goals: efficient and accurate predictions of microstructure evolution, mechanical properties, defects, etc.
Microstructure-based mechanical property predictions [Saha et al, IMMI, 2021]
Stochastic modeling
Goals: stochastic computational predictions of melt pool variability, surface roughness, porosity, etc.
Stochastic thermal fluid analysis for surface roughness and porosity predictions [Li et al, AM, 2024]
Publications:
Lu et al., Extended tensor decomposition model reduction methods: Training, prediction, and design under uncertainty, Computer Methods in Applied Mechanics and Engineering, 2024.
Li et al., Statistical Parameterized Physics-Based Machine Learning Digital Shadow Models for Laser Powder Bed Fusion Process, Additive Manufacturing, 2024.
Lu et al., Reduced order machine learning finite element methods: concept, implementation, and future applications, Computer Modeling in Engineering & Science, 2021.
Saha et al., Microscale Structure to Property Prediction for Additively Manufactured IN625 through Advanced Material Model Parameter Identification, Integrating Materials and Manufacturing Innovation, 2021.
Lu et al., Adaptive hyper reduction for additive manufacturing thermal fluid analysis, Computer Methods in Applied Mechanics and Engineering, 2020.
Phase field modeling of fracture
We developed a phase field modeling framework for quasi-static fracture of brittle materials. This development includes a robust solution solver for overcoming the unstable cracking and an efficient strategy for imposing the irreversible damage field. The developed phase field method has been applied to various fracture problems and the simulated fracture patterns showed a good agreement with experimental observations.
Publications:
Lu et al., An efficient and robust staggered algorithm applied to the quasi-static description of brittle fracture by a phase-field approach, Computer Methods in Applied Mechanics and Engineering, 2020.
Reduced order modeling for welding
We developed a data-driven reduced order surrogate modeling technique, namely High Order Proper Generalized Decomposition (HOPGD), for real time predictions of the welding process. The reduced order surrogate models serve as digital twins to the physical welding process and can provide real time predictions for residual stresses and distortions. The digital twin model can avoid solving repetitively the computationally expensive nonlinear space-time multiphysics model and can be used for performing the challenging high dimensional parametric studies, including process condition optimization, material calibration, and uncertainty quantification, etc.
Digital twins for accelerated process optimization, material calibration, uncertainty quantification, etc.
Publications:
Lu et al., Datadriven HOPGD based computational vademecum for welding parameters identification, Computational Mechanics, 2019.
Lu et al., Adaptive sparse grid based HOPGD: Towards a nonintrusive strategy for constructing space-time welding computational vademecum, International Journal for Numerical Methods in Engineering, 2018.
Lu et al., Multi-parametric space-time computational vademecum for parametric studies: Application to real time welding simulations, Finite Elements in Analysis and Design, 2018.
Lu et al., Space–time POD based computational vademecums for parametric studies: application to thermo-mechanical problems, Advanced Modeling and Simulation in Engineering Sciences, 2018.